Automation is Keeping Up with Demand
Automation is – A series on the challenges and opportunities in food logistics.
July 29, 2021
Challenge #2 – The Cold Chain in the Era of Instant Gratification
As product variety grows, so does the complexity of the cold chain.
Americans consume roughly the same amount of food and beverages as they did five years ago. What has changed is the number of options. Take yogurt, for example. There are now almost twice as many types of yogurts available as there were five years ago, which means there are twice as many options for retailers to stock.
In our world, SKU proliferation has necessitated a fundamental shift in pallet picking. The demand for variety has shifted product movements from full pallets to a higher rate of mixed-SKU pallets.
- 2015 saw an 18.5% increase in the number of SKUs handled by the average warehouse or order fulfillment operation (Source).
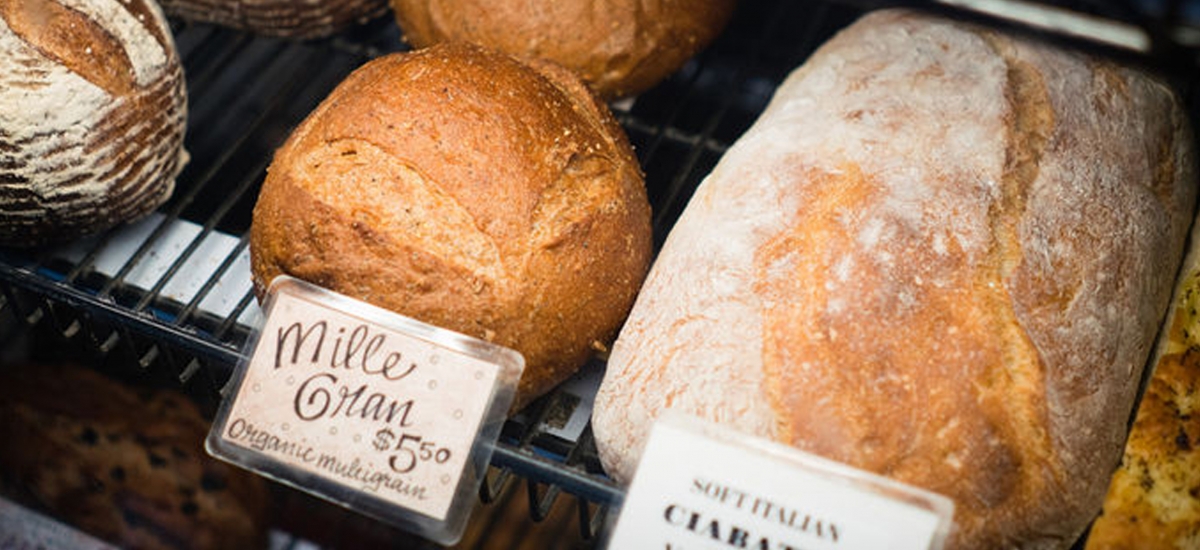
An explosion in consumer choices means rethinking how we deliver
The COVID-19 impact on the economy hastened the arrival of a part of our industry that had previously felt more niche than essential: The mainstream acceptance and consumer demand for same-day and two-day delivery by giants, such as Amazon, Walmart and Target, brought to the forefront an expectation for instant gratification – an expectation that accelerates all aspects of the food supply chain to accommodate expedited delivery.
E-commerce and direct-to-consumer are now major channels of demand. Changes in shopping behaviors have increased throughput requirements of the upstream warehouses due to this abundance of product choices as well as delivery method choices (e.g., in-store shopping, curbside service, direct to consumer, meal kits, etc.).
This complexity is being passed on to the end-user: the grocer. As direct-to-consumer grocery mechanisms, such as app-based delivery services, force the back rooms of retail stores to operate as mini distribution centers, stores now need more and more frequent and varied deliveries.
Solution 1: Using autonomous pallet pickers
Before automation was incorporated into the rainbow pallet-building process, a worker would drag a pallet through a warehouse and manually pull every single box from source pallets. The introduction of automated layer pickers allows a facility to automate up to 96% of the volume shipped through the warehouse. With automated layer picking technology, rainbow pallets are created by robotically removing layers of single SKU pallets to create multilayered full pallets.
- Walking and manually picking orders can account for more than 50% of the time associated with picking.
Automation in Action: The Fully Automated Warehouse.
A large regional distribution center for several customers, our Allentown, Pennsylvania, facility moves approximately 200 trucks of product in and out daily, encompassing nearly 4 million pounds per day. As vendors have added more choices/SKUs to their offerings, and consumers have become more specific in their orders, growth in order variability has significantly increased the amount of case picking or partial pallets needed to fulfill orders.
To alleviate the stress of this new demand, we are implementing automation in high-throughput areas of the warehouse. More specifically, we are installing a layer picker machine and multiple automated guided vehicles (AGVs) to reduce the amount of labor utilized in the case picking function.
The layer picker and the AGVs will work as part of the overall inbound/outbound flow of product, but the loading and unloading of trucks will continue to be done by humans on material handling equipment. The automation will come into play as AGVs will retrieve inbound pallets from staging areas on our dock, will put/pull pallets into/out of racking, will feed the layer picker with the needed product and will place outbound pallets in staging areas on the dock. The layer picker will help to reduce the pressure of unpredictable labor markets and fluctuating consumer demands.
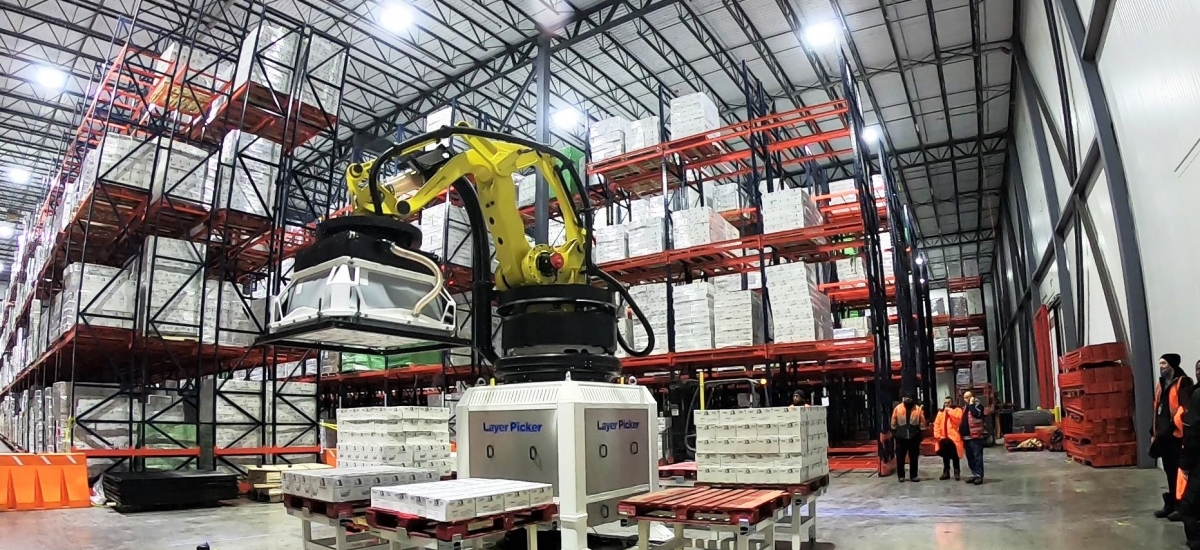
Solution 2: Doing more with less
Last-mile storage is physically shifting the supply chain landscape.
As e-commerce continues to explode and more consumers gravitate toward direct-to-consumer service, the last-mile storage facility is quickly becoming a more integral part of the food supply chain. These warehouses are often built vertically in densely populated urban areas where traditional, large footprint distribution centers would be impractical and cost prohibitive. Automation removes those limits by utilizing programmed lifts that are built into the design of the warehouse.
The sky is the limit.
Currently, the tallest Lineage storage facility stands 140 feet tall. Normally, our manually operated warehouses are approximately 35 feet tall due to limitations imposed by forklifts and fire protection. With the automated designs, the facility can store approximately five times as much inventory as a manual facility with the same footprint.
In Challenge #1 we established that automation is a solution for the current labor market. Maintaining the safety and efficiency of the global food supply chain during a labor crisis poses new challenges, especially with ever-changing consumer demand. By advancing the technology we use in our operations, we can alleviate the impact of a labor shortage and keep the food supply chain moving. In our next post in the series, we’ll discuss the challenge of becoming more sustainable and achieving energy savings across the supply chain.
Sources:
Michel, R. (2015, November 9). 2015 Warehouse & DC Operations Survey Results. Supplychain247.com. http://www.supplychain247.com/article/2015_warehouse_dc_operations_survey_result