Automatisering is niet iets voor iedereen
Een vervolg op de serie: Automatisering is
03 februari 2022
Niet alle geautomatiseerde magazijnen zijn hetzelfde. Om de juiste hoeveelheid en soorten automatisering aan onze faciliteit toe te voegen, is het essentieel om de behoeften en organisatorische resultaten van onze klanten te begrijpen. In principe zijn er drie brede benaderingen van automatisering als het gaat om integratie in de koudeketen.
Het volledig geautomatiseerde magazijn.
Het volledig geautomatiseerde magazijn is een faciliteit die wordt gerund door grootschalige, volledig geïntegreerde robotsystemen, uitgerust met talloze kranen en rijen transportbanden voor inkomende ontvangst en het opbouwen van pallets. Hoewel er in elke faciliteit altijd een toezichthoudende menselijke component aanwezig zal zijn, is 95% van onze volledig geautomatiseerde opslag 'no-touch'.
Deze nieuwe magazijnen, in combinatie met onze algoritmen en software, zorgen voor een grote toename in opslagdichtheid, doorvoer en capaciteit. Als voordeel hebben deze faciliteiten geen last van de hoogtebeperkingen die vorkheftrucks opleggen aan handmatige magazijnen. Hogere gebouwen bieden flexibiliteit in waar we een magazijn kunnen plaatsen, inclusief dichtbevolkte gebieden.
Lineage automatisering in actie: Bergen op Zoom
Met een doorvoercapaciteit van 5.500 inkomende en uitgaande pallets per dag en een maximale opslagcapaciteit van 180.000 pallets, biedt onze vestiging in Bergen op Zoom, Nederland, een kijkje in de toekomst van de automatisering van de koudeketen. Bergen op Zoom heeft slechts 15 vorkheftruckchauffeurs per dienst.
De vestiging in Bergen op Zoom is ontstaan als gevolg van onze relatie met een Europese grondstoffenproducent. In samenwerking met onze partner hebben we een elektronische gegevensuitwisseling (EDI) ontwikkeld die, in combinatie met de software van ons magazijnbeheersysteem en vervolgens ontvangen door ons I-point (inspectiepunt), een volledig geautomatiseerd proces mogelijk maakt van inkomende vrachtwagen tot uitgaande vrachtwagen.
We bereiken zo'n ongelooflijke verwerkingscapaciteit met ongeveer 100 teamleden, waaronder één procescontroller. De procescontroller fungeert in wezen als een luchtverkeersleider in het magazijn en is er verantwoordelijk voor dat de duizenden palletposities op het uitgebreide systeem van transportbanden in het magazijn goed gesynchroniseerd zijn. Als er zich een verstoring voordoet, is het de taak van de procescontroller om ervoor te zorgen dat er geen vertraging optreedt voor de klant.
Naarmate geautomatiseerde processen opschalen en kunnen voortbouwen op andere processen, zal Bergen op Zoom op een dag de totale opslagcapaciteit kunnen uitbreiden tot 280.000 palletposities. Dedicated gebouwen zoals de faciliteit in Bergen op Zoom kunnen op maat gemaakte automatisering, specificaties, ontwerpen en workflows toepassen op basis van de specifieke behoeften van een klant. De ontwerpspecificaties van een speciale faciliteit zijn veel minder speculatief .

Een gemengde aanpak.
Niet alle organisaties kunnen het zich veroorloven om te investeren in de bouw van nieuwe, volledig geautomatiseerde structuren. Bestaande gebouwen aanpassen met verschillende automatiseringsmodi biedt veel van dezelfde voordelen tegen lagere kosten. Mixed-mode automatisering is een combinatie van mensafhankelijke taken met een geautomatiseerde component. Mixed mode kan magazijnen helpen die worstelen met arbeids- en doorvoerproblemen door processen te automatiseren zonder de algehele activiteiten te verstoren.
Voor het succesvol ontwerpen van mixed-mode automatisering moet elke taak en elke workflow worden gezien als een programmeerbare functie. Ongeacht de menselijke of geautomatiseerde component kunnen workflows via dit proces in kaart worden gebracht en gesynthetiseerd. De juiste software kan bepalen welke functies het meest gebaat zijn bij een conversie naar een geautomatiseerd proces.
Lineage automatisering in actie: Allentown, Pennsylvania
Als proeftuin voor mixed mode besloot Lineage een deel van onze vestiging in Allentown, Pennsylvania te reengineeren. Als een groot regionaal distributiecentrum voor verschillende klanten, vervoert Allentown dagelijks ongeveer 200 vrachtwagens met producten, wat neerkomt op bijna 4 miljoen kilo per dag. Naast de impact van het tekort aan arbeidskrachten die in de hele sector voelbaar is, hebben klanten meer keuzes/SKU's toegevoegd aan hun aanbod en consumenten zijn op hun beurt specifieker geworden in hun bestellingen. Deze groei in ordervariabiliteit heeft de hoeveelheid case picking of gedeeltelijke pallets die nodig zijn om orders uit te voeren aanzienlijk vergroot.
Case picking is van oudsher een zeer handmatig en traag proces dat veel arbeid vergt. Om de stress van de nieuwe eisen te verlichten, implementeren we automatisering in het hele magazijn. Meer specifiek maken we gebruik van een laagjespickermachine en meerdere AGV's (automatisch geleide voertuigen) om de hoeveelheid arbeid te verminderen die nodig is voor het picken van kratten en het verplaatsen van pallets.
De laagverzamelaar en de AGV's werken als onderdeel van de totale inkomende/uitgaande productstroom. Mensen op MHE (material handling equipment) blijven vrachtwagens laden en lossen. AGV's zullen automatisch inkomende pallets ophalen uit stellingen op onze kade, pallets in stellingen plaatsen en uit stellingen halen, de laagpicker het benodigde product geven en uitgaande pallets in stellingen op de kade plaatsen. De laagjespicker zal het menselijke element van het picken van kratten vervangen voor tienduizenden kratten per dag.
Door bepaalde geautomatiseerde mogelijkheden te implementeren, verwachten we tal van voordelen, zoals minder arbeidsuren, meer veiligheid, een betere kwaliteit en een betere klantenservice. We verwachten ook de fouten te minimaliseren die veroorzaakt worden door het verkeerd picken van producten. Tot slot zouden de schommelingen in onze service moeten afnemen door een consistente aanwezigheid van automatisering, omdat we minder risico lopen op een tekort aan arbeidskrachten als gevolg waarvan de service afneemt .
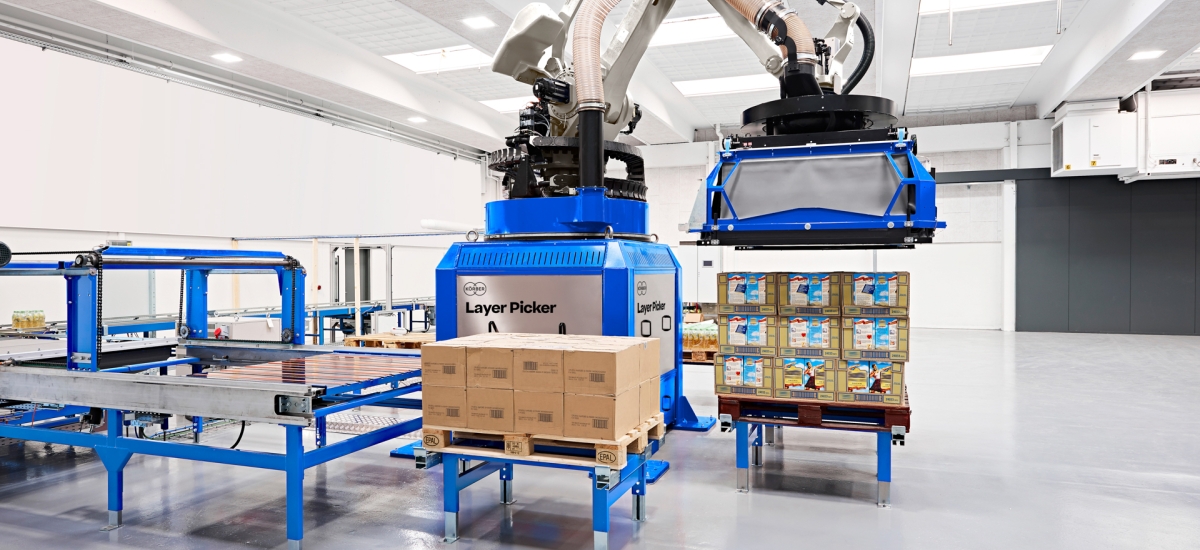
Selectief toevoegen aan bestaande processen.
Automatiseringsniveaus (d.w.z. de hoeveelheid automatisering in een magazijn) worden vastgesteld op basis van de taken die moeten worden uitgevoerd. Deze taken worden bepaald door de klanten die worden bediend, dus automatiseringsontwerpen moeten worden gemaakt om te anticiperen op klanten, marktbehoeften en bewegingen in de toeleveringsketen.
Elke geautomatiseerde toepassing vermindert uiteindelijk de workflow. In een geautomatiseerde werkomgeving kunnen we geautomatiseerde functies op elk moment verminderen, maar de technologische mogelijkheden en de capaciteit van de apparatuur beperken ons vermogen om functies toe te voegen. Traditioneel betekende meer werk gewoon meer arbeid, maar met automatisering is er een plafond. Er zijn maar een beperkt aantal verhuizingen per uur die een bepaalde set hardware kan uitvoeren; dus voordat we een geautomatiseerd proces implementeren, moeten we de workflow en beperkingen begrijpen.
De beste aanpak kiezen.
Automatisering is een dienst die uiteindelijk de toekomst van de koudeketen zal veranderen. Een van de vele gunstige aspecten van automatisering is de hoeveelheid flexibiliteit die het mogelijk maakt op onze magazijnvloer. Terwijl individuele aspecten van geautomatiseerde systemen ontworpen zijn om één specifieke taak uit te voeren, maakt het concept van automatisering talloze combinaties van individuele taken mogelijk om grootschalige toepassingen mogelijk te maken. De beste manier om automatisering in de wereldwijde koudeketenomgeving te implementeren, is door de fundamentele basisverschillen van elk niveau te overwegen en te kijken hoe het de efficiëntie en activiteiten zal beïnvloeden .
Klik hier om de rest van de serie te lezen: Automatiseren is.